
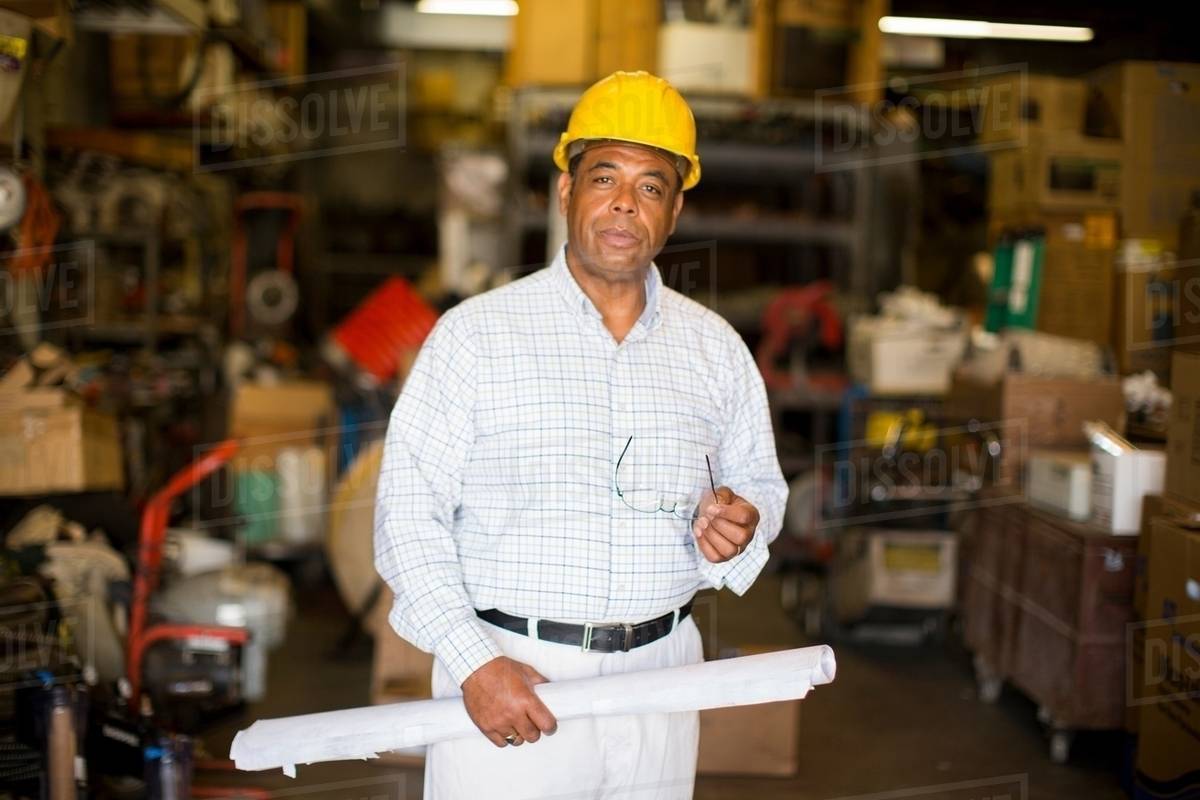
The type of warehouse equipment you use is a big consideration when creating a warehouse floor plan. Allocate space for equipment and workstations
WAREHOUSE BLUEPRINT BACKGROUND SOFTWARE
Whether you use a software program or simple grid paper, drawing a schematic at scale will help you visualize workflows and determine the best locations for storage, receiving, sorting, packaging and shipping. Visuals like warehouse floor plan schematics and design software are helpful for determining the best floor plan design for flow. For example, plan space for sorting near packaging and shipping areas, so that products don’t have to travel across the facility for each subsequent step. Plan your warehouse floor plan so that sequential activities are located nearby. Warehouse blueprints that allow for the uninterrupted flow of people, materials, and equipment support efficiency by reducing heavy traffic congestion in aisles. Design your warehouse floor plan for uninterrupted flow Redesigning your warehouse floor plan to incorporate ample cross aisles helps to reduce the long walk. Likewise, long rows of warehouse racks with few to no cross-aisles often means your associates are spending more time walking than necessary. If your associates are frequently retrieving products from bulk storage and moving them to replenish picking locations, moving those high-velocity items to the floor can reduce the number of touches – a key factor in efficient warehouse operations. Even the most optimized pick routes should be reevaluated periodically, as product lines, storage organization and picking methods can change over time.Īnother common issue is storing frequently picked items in bulk storage areas. For example, one common warehouse layout issue is poorly configured pick faces, leading associates to back-track to retrieve items instead of following more efficient pick routes.

If you’re reorganizing an existing warehouse, identifying inefficiencies in your current design is a good starting point. Consider the type of inventory you store, product sizes and other physical characteristics, how much stock you’ll store and where inventory arrives and departs the facility. The first step in creating a warehouse floor plan to maximize efficiency is to consider your needs, such as the order fulfillment methods you plan to implement, space utilization and storage requirements. While there’s no one-size-fits-all floor plan, there are a few best practices to keep in mind that will help you create a warehouse floor plan that maximizes efficiency. For another facility, however, extra-wide aisles may take up much-needed floor space that would be better used for storage. Extra-wide aisles may work for one facility that has a constant two-way flow of traffic consisting of both human associates and heavy equipment. There’s no universal warehouse floor plan that works for every warehouse operation. A warehouse floor plan that’s designed to maximize efficiency, on the other hand, supports streamlined workflows and processes that help warehouse operators meet their goals. A floor plan that makes navigation difficult or makes it necessary for warehouse associates to travel long distances to complete common tasks can impact all of these workflows, reducing the overall efficiency of your operation. There are a variety of factors that can hinder the flow of products through a warehouse, from inadequate replenishment processes to order picking inefficiencies. Every warehouse operator’s goal is to ensure that goods flow efficiently in and out of the facility.
